Pierwsza metalowa rama rowerowa opracowana i wyprodukowana z zastosowaniem technologii druku 3D przez firmę Renishaw dla Empire Cycles
Firma Renishaw, jako jedyny w Wielkiej Brytanii producent maszyn do wytwarzania przyrostowego na bazie metalu, drukujących metalowe części, we współpracy z wiodącą brytyjską firmą zajmującą się projektowaniem i produkcją rowerów, wyprodukowała pierwszą na świecie metalową ramę rowerową w technologii druku 3D.
Empire Cycles to wyjątkowa brytyjska firma projektowo-produkcyjna z siedzibą w południowo-zachodniej Anglii. Firma z pasją korzysta z wielu rozwiązań inżynierskich do tworzenia wiodących produktów. Firma oferuje na całym świecie innowacyjne projekty dla sportowców uprawiających kolarstwo górskie i zjazdowe Współpraca Renishaw i Empire Cycles pozwoliła zoptymalizować projekt roweru pod kątem technologii wytwarzania przyrostowego, eliminując wykonanie szeregu powierzchni, które wymagałyby specjalnych, zbędnych struktur wzmacniających.
Firma Empire Cycles zaprojektowała rower górski wykorzystując technologię wytwarzania przyrostowego firmy Renishaw oraz topologiczną optymalizację, co pozwoliło na wyprodukowanie tytanowej ramy, która jest zarówno wytrzymała, jak i lekka– nowa rama jest ok. 33% lżejsza od oryginału. Rama rowerowa została wytworzona przyrostowo ze stopu tytanu w częściach i zespolona w całość. Zapewnia to szereg korzyści:
Swoboda projektowania
- Szybki proces iteracyjny, elastyczność w zakresie dokonywania poprawek konstrukcyjnych w procesie produkcji
- Możliwość tworzenia kształtów uzyskiwanych poprzez topologiczną optymalizację
- Szerokie możliwości w zakresie modyfikacji, dostosowywania, budowy „na miarę” – stapianie laserowe proszków metalicznych pozwala na produkcję pojedynczych egzemplarzy, jak również części seryjnych
Konstrukcja
- Skomplikowane kształty z wewnętrznymi elementami wzmacniającymi
- Puste (wydrążone) struktury
- Wbudowane cechy indywidualne, jak na przykład nazwisko właściciela
Wytrzymałość wykonania, stop tytanu
- Wspornik siodełka jest lżejszy o 44% niż wersja wykonana ze stopu aluminium
- Niezwykła wytrzymałość – zgodnośc z wymaganiami normy EN 14766
- Odporność na korozję i długa żywotność
Jak wygląda kwestia ciężaru?
Pełna rama została przygotowana w częściach ze wspornikiem siodła na jednym stole roboczym i zmontowana w ramach jednej operacji. Stopy tytanu charakteryzują się większą gęstością od stopów aluminium, z względnymi gęstościami odpowiednio na poziomie ok. 4 g/cm3 i 3 g/cm3. Dlatego, aby wytworzyć tytanową część lżejszą od jej aluminiowego odpowiednika, należy znacząco zmodyfikować projekt i usunąć nadmiar materiału, który nie wpływa na wynikową wytrzymałość części.
Oryginalny aluminiowy wspornik siodełka waży 360 g, zaś wydrążona wersja tytanowa waży 200 g, czyli o 44% mniej. To dopiero pierwszy krok; dalsza analiza i testy umożliwić mogą większą redukcję ciężaru. Oryginalna rama rowerowa waży 2100 g. Zmiany konstrukcyjne pod kątem zastosowania technologii wytwarzania przyrostowego pozwoliły na spadek jej ciężaru do 1400 g, czyli redukcję o 33%.
Dostępne są oczywiście lżejsze rowery z ramą zbrojoną włóknami węglowymi, jednak zdaniem Chrisa Williamsa, dyrektora zarządzającego w firmie Empire Cycles według badań „trwałość włókna węglowego nie może równać się z trwałością metalu. Wytrzymałość i trwałość tychże włókien spełnia wymagania konstrukcyjne stawiane ramom rowerów szosowych. Jeśli jednak spróbujemy zjeżdżać takim rowerem po górskim stoku ryzykujemy uszkodzeniem włókien tworzących ramę. Wręcz przesadnie dbam o konstrukcję moich rowerów, by uniknąć późniejszych roszczeń gwarancyjnych”. Wręcz przesadnie dbam o konstrukcję moich rowerów, by uniknąć późniejszych roszczeń gwarancyjnych”.
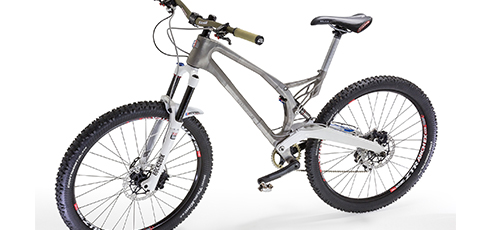
Jak wyglądało zarządzanie projektem?
Przed podjęciem współpracy z Renishaw, Chris miał już wcześniej okazję skorzystać z technologii druku 3D do wykonania pełnowymiarowej repliki swojego roweru. Firma Renishaw zgodziła się początkowo zoptymalizować i wyprodukować wyłącznie wspornik siodła, jednak gdy zakończyło się to powodzeniem, stwierdziła, że warto wyprodukować całą ramę. Chris zaktualizował swój projekt zgodnie ze wskazówkami zespołu technicznego Renishaw w zakresie procesu wytwórczego, a rama została podzielona na części, by w pełni wykorzystać 300 mm wysokość roboczą urządzenia AM250.
Kluczową korzyścią dla Empire Cycles są zalety w zakresie wydajności, jakie uzyskać można dzięki tej metodzie wytwarzania. Projekt posiada wszystkie zalety konstrukcji typu „skorupowego” ze stali tłoczonej stosowanych w motocyklach i samochodach, bez konieczności ponoszenia nakładów inwestycyjnych na oprzyrządowanie, które dla małych producentów są ograniczeniem. Liczymy na dalszy rozwój tego projektu. Ponieważ nie jest wymagane jakiekolwiek oprzyrządowanie, projekt może być z łatwością stale udoskonalany. Na koszt podzespołów wpływa ilość potrzebnego materiału a nie złożoność konstrukcji. Dlatego też, niektóre lekkie części wykonać można przy minimalnych nakładach.
W wyniku badań w zakresie metod spajania wybrano firmę Mouldlife na dostawcę spoiwa oraz uzyskano wsparcie techniczne specjalistów z firmy 3M w zakresie przeprowadzenia testów. Zamierzamy rozwijać projekt wspólnie, by dążyć do stopniowych usprawnień w zakresie metod spajania, jak np. specyficznej obróbki powierzchni. Koła, układ napędowy i podzespoły wymagane do skompletowania roweru zostały dostarczone przez firmę Hope Technology Ltd. Projekt ten pokazuje, że wspaniałe rezultaty można osiągać w efekcie ścisłej współpracy z klientem. Jeśli posiadają Państwo podzespoły, które mogłyby zyskać dzięki technologii wytwarzania przyrostowego, prosimy o kontakt z lokalnym biurem Renishaw, w celu uzyskania dodatkowych informacji.
Tutti i documenti e le immagini sono protetti da copyright di Renishaw